We Are Paradoxx - A Case Study
The Client
We Are Paradoxx is a cosmetics company that produces a wide range of personal care products, including hair conditioners. They required an efficient, reliable, and high-quality packaging solution that could withstand the rigors of filling, storage, and transportation while maintaining the integrity, finish, and quality of their product.
To achieve this, they approached TubeWorx to fill printed collapsible aluminium tubes with their hair conditioner, utilizing our state-of-the-art filling machines and industry expertise.
Why Aluminium?
Aluminium is an excellent choice for packaging due to its lightweight, durable, and corrosion-resistant properties. It provides superior protection for the product while being an environmentally friendly alternative to plastic.
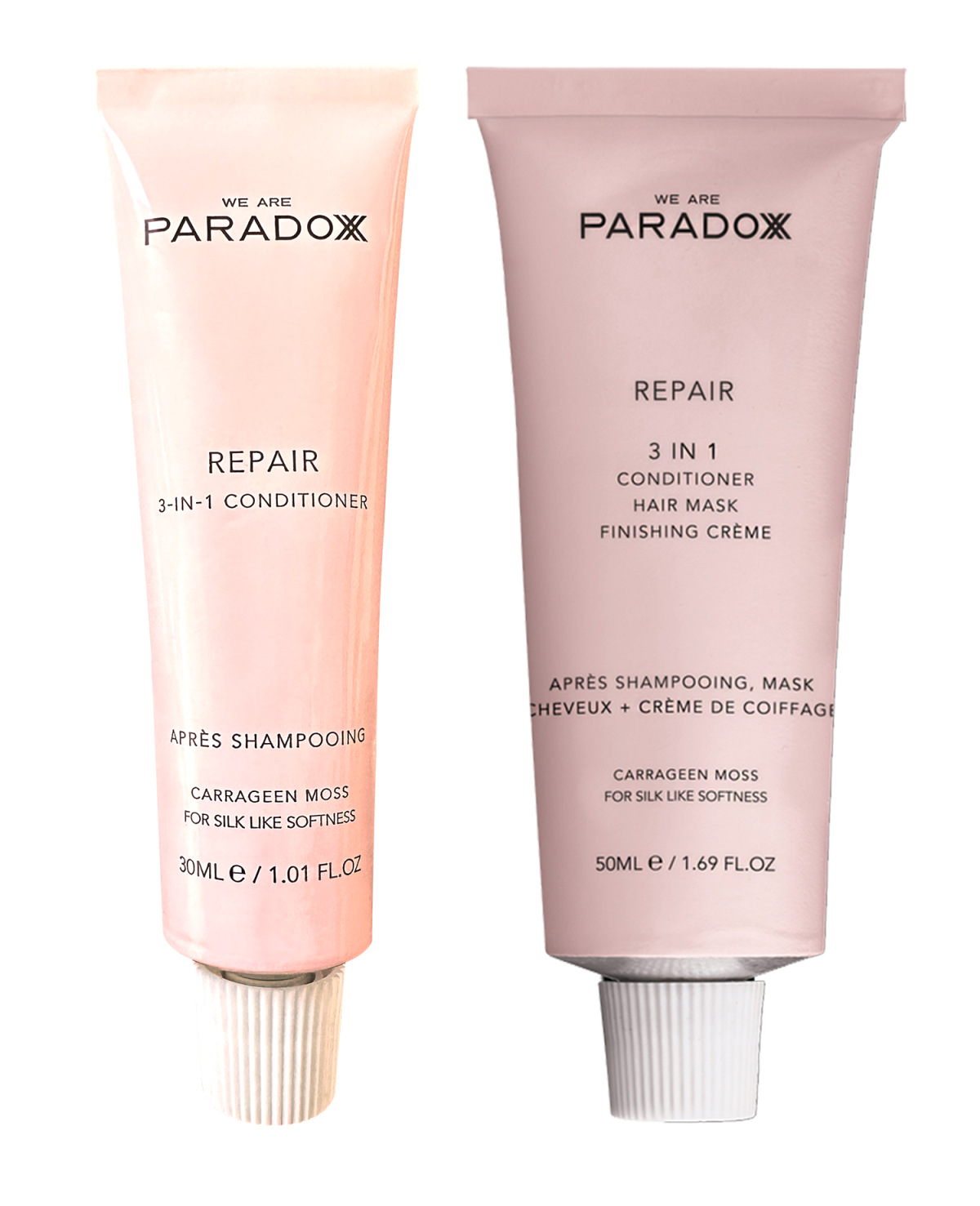
The Challenge
The task was to efficiently and accurately fill over 200,000 printed aluminium tubes with the client’s hair conditioner.
The process needed to be:
• Hygienic – to ensure product safety
• Precise – to maintain consistency in fill volume
• Efficient – to meet high production demands
• Reliable – to protect the product during storage and transportation
Materials and Logistics
To complete the project, a well-coordinated supply chain was essential.
As these materials arrived separately, TubeWorx coordinated deliveries to ensure all components were available on time, allowing production to run smoothly.
• Hair Conditioner: Delivered in IBC tanks from the chemical manufacturer
• Printed Aluminium Tubes: Supplied directly from the tube manufacturer
• Box Packaging: Provided by the client’s packaging supplier
As these materials arrived separately, TubeWorx coordinated deliveries to ensure all components were available on time, allowing production to run smoothly.
The Solution
Tubeworx approached the challenge by following a step-by-step process:
Tubeworx team worked closely with the client to to ensure the job can be done in an efficient, safe and reliable way. Tubeworx did tests with the hair conditioner to make sure it was able to pass through the filling machine. Also work closely with the client over the sizes of the aluminium tubes required, that the tubes met all the necessary requirements and were easy to fill, seal, and dispense while effectively containing the product within.
Preparation
Before filling, our team:
• Conducted product compatibility tests to ensure the hair conditioner could pass through our filling machines efficiently
• Worked closely with the client to determine the correct tube specifications, ensuring they were easy to fill, seal, and dispense
• Scheduled coordinated deliveries of IBC tanks, tubes, and packaging to maintain a seamless workflow
• Ensured storage capacity for up to 40 pallets of raw materials and filled products
The filling area and machinery were thoroughly cleaned and calibrated to meet the Good Manufacturing Practices under Regulation (EC) No 2023/2006 in conjunction with Tubeworx Hazard Analysis and Critical Control Points Framework to ensure high hygiene and quality standards before production began.
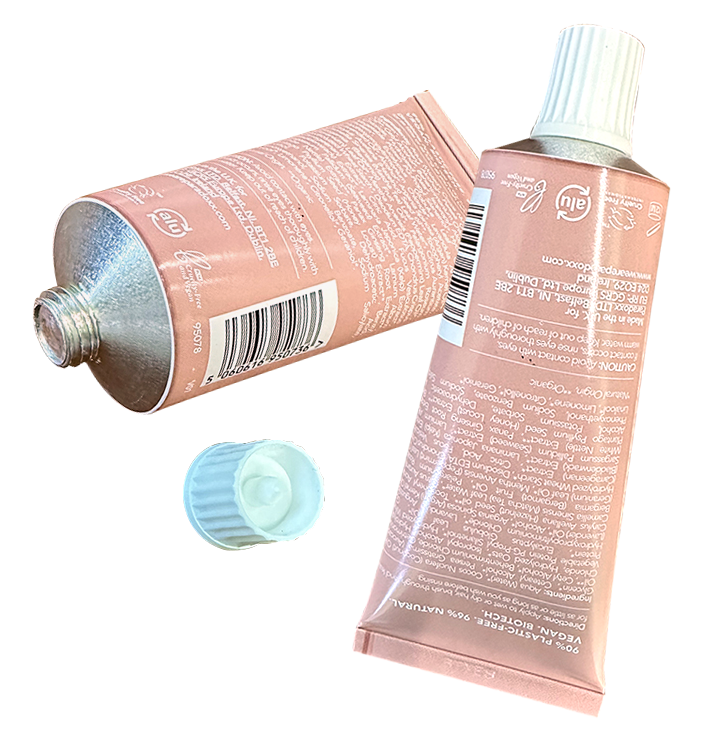
Filling and Sealing
The hair conditioner was transferred directly from the IBC tank into the filling machine’s hopper using a high-powered pump. Our fully automated filling machine then:
The precise filling and crimping process ensured zero leakage, minimal waste, and maximum efficiency.
• Accurately dispensed the conditioner into aluminium tubes at a speed of over 30 tubes per minute
• Sealed each tube immediately after filling to maintain hygiene and prevent contamination
• Stamped each tube with a batch code for full traceability and quality control
The precise filling and crimping process ensured zero leakage, minimal waste, and maximum efficiency.
Inspection and Packing
• As the filled tubes moved along the conveyor, each one underwent a final quality inspection
• Tubes were immediately packed into pre-made boxes, each containing 144 tubes with dividers to prevent damage during transportation
• Pre-packed boxes were loaded onto pallets, ready for distribution
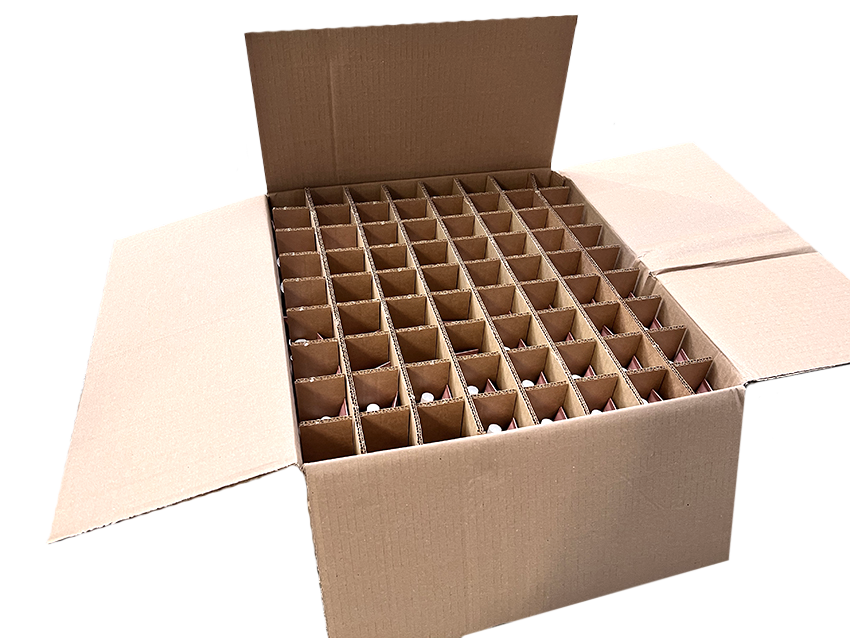
Delivery and Logistics
The client required deliveries to multiple locations, with some shipments managed by them and others arranged by TubeWorx. Our team ensured efficient coordination and on-time dispatch to meet all delivery requirements.
Outcome
• 200,000 aluminium tubes filled accurately, efficiently, and on schedule
This project highlighted the importance of advanced automation, meticulous planning, and a reliable supply chain in the tube-filling industry. TubeWorx delivered a premium, market-ready product while optimizing production costs and efficiency.
• Zero spillage or contamination thanks to our rigorous quality control process
• Seamless logistics and packaging integration
• High client satisfaction with the product’s quality and production efficiency.
This project highlighted the importance of advanced automation, meticulous planning, and a reliable supply chain in the tube-filling industry. TubeWorx delivered a premium, market-ready product while optimizing production costs and efficiency.
Conclusion
Filling printed aluminium tubes with hair conditioner requires careful preparation, logistics coordination, and precise execution. By utilizing state-of-the-art technology and automation, TubeWorx ensures:
• Consistent product quality
• Efficient production timelines
• Hygienic and safe processing
• Cost-effective and scalable solutions
Looking for a trusted partner for your tube-filling needs? Contact TubeWorx today!
Looking for a trusted partner for your tube-filling needs? Contact TubeWorx today!
+44 (0)1223 625253
sales@tubeworx.co.uk
Tubeworx Ltd. Haynes' Yard, Swaffham Road, Cambridge, CB25 9EZ