Life Supplies
Life Supplies - A Case Study
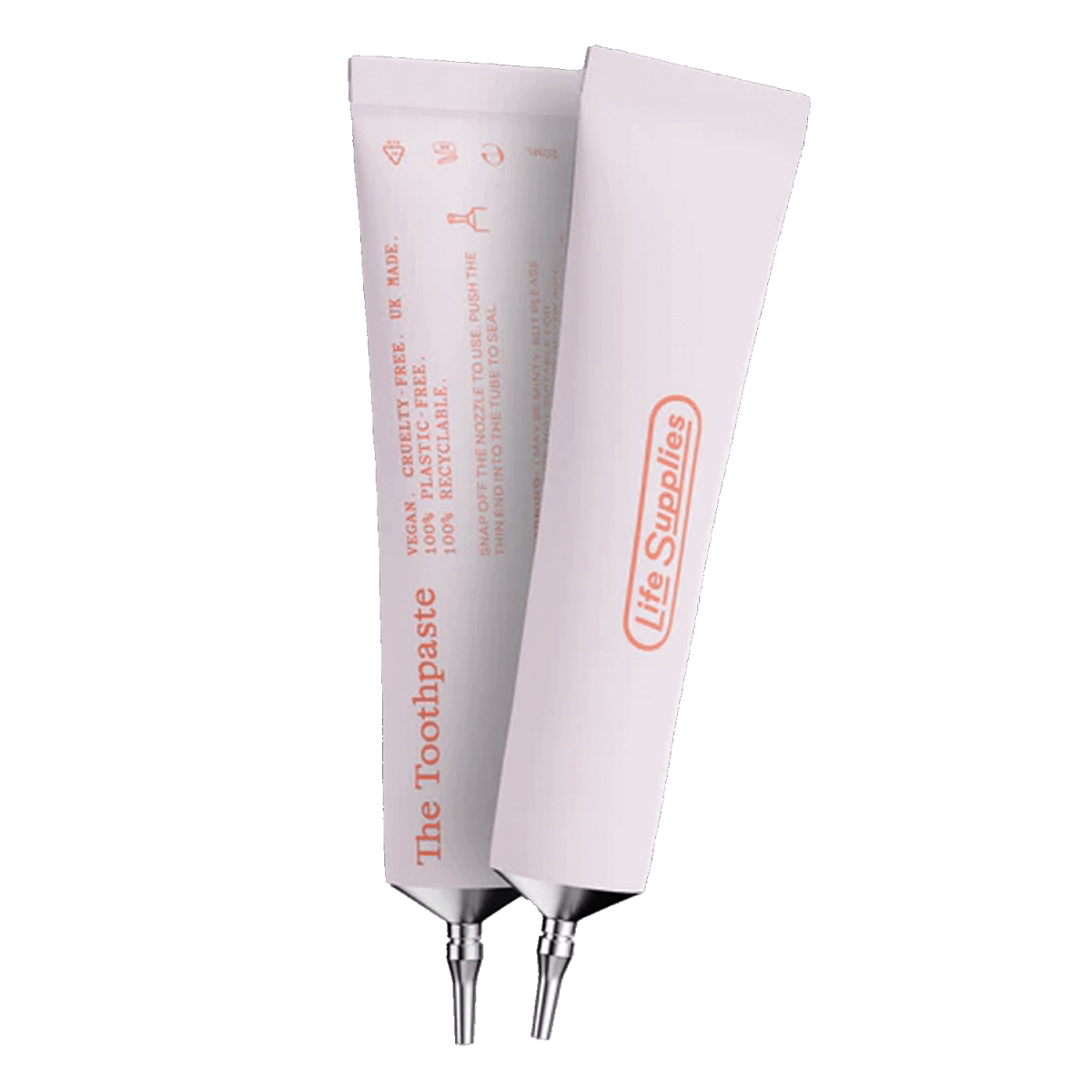
The Client
Life Supplies is a sustainable personal care brand committed to eco-friendly, plastic-free packaging. As part of their zero-plastic approach, they use collapsible aluminium tubes instead of traditional plastic tubes, reducing environmental impact while offering a more premium look and feel.
For their latest toothpaste production, they required a fast, precise, and reliable filling solution for 15,000 aluminium tubes within a strict one-month timeframe.
This was TubeWorx’s first project with Life Supplies, with the potential for future production runs. The challenge was not only to meet the deadline but also to resolve an overfilling issue they had experienced in previous runs with other suppliers.
Through meticulous planning, machine calibration, and rapid problem-solving, TubeWorx completed the project in just three weeks—one week ahead of schedule—ensuring Life Supplies avoided stock shortages.
For their latest toothpaste production, they required a fast, precise, and reliable filling solution for 15,000 aluminium tubes within a strict one-month timeframe.
This was TubeWorx’s first project with Life Supplies, with the potential for future production runs. The challenge was not only to meet the deadline but also to resolve an overfilling issue they had experienced in previous runs with other suppliers.
Through meticulous planning, machine calibration, and rapid problem-solving, TubeWorx completed the project in just three weeks—one week ahead of schedule—ensuring Life Supplies avoided stock shortages.
The Challenge
Life Supplies approached TubeWorx with a strict one-month deadline to fill, seal, and package 15,000 aluminium tubes of toothpaste. However, to prevent stock shortages, the timeline was tightened, and the entire job needed to be completed in just three weeks. While speed was critical, the project also presented several technical and logistical challenges that had to be addressed to ensure a high-quality, problem-free production run.
One of the key issues was overfilling. Life Supplies had previously experienced a problem where toothpaste would squirt out when the consumer first opened the tube. The cause of this was identified as excessive fill levels. To prevent this from happening again, TubeWorx had to diagnose the issue, establish the correct fill level, and recalibrate the filling machines accordingly.
There were also challenges with materials and tube design.
On the packaging side, Life Supplies had sourced their own materials, but to stay within the tight timeframe, TubeWorx had to pre-assemble the individual boxes before filling began. The tubes were packed into these boxes immediately after filling and then bulk-packed onto pallets for shipment. Since the materials arrived separately, TubeWorx also managed the coordination of deliveries and the return of any remaining packaging and tubes after production.
Despite these obstacles, TubeWorx successfully adapted by making fast equipment modifications, refining the filling process, and ensuring a seamless logistics workflow. This allowed the entire production run to be completed one week ahead of schedule, ensuring Life Supplies could continue fulfilling orders without any stock shortages.
One of the key issues was overfilling. Life Supplies had previously experienced a problem where toothpaste would squirt out when the consumer first opened the tube. The cause of this was identified as excessive fill levels. To prevent this from happening again, TubeWorx had to diagnose the issue, establish the correct fill level, and recalibrate the filling machines accordingly.
There were also challenges with materials and tube design.
• The toothpaste arrived in an IBC tank with a non-standard fitting, which was incompatible with our filling equipment. This required an urgent search for an adapter to avoid production delays.
• The aluminium tubes featured a snap-off nozzle instead of a traditional screw cap, making them more fragile during handling. We had to carefully adapt our filling process to prevent damage while ensuring a perfect seal.
• The tube height was not optimal for a standard crimp, meaning we needed to adjust our crimping mechanism to achieve a secure and visually consistent finish without affecting the printed branding.
On the packaging side, Life Supplies had sourced their own materials, but to stay within the tight timeframe, TubeWorx had to pre-assemble the individual boxes before filling began. The tubes were packed into these boxes immediately after filling and then bulk-packed onto pallets for shipment. Since the materials arrived separately, TubeWorx also managed the coordination of deliveries and the return of any remaining packaging and tubes after production.
Despite these obstacles, TubeWorx successfully adapted by making fast equipment modifications, refining the filling process, and ensuring a seamless logistics workflow. This allowed the entire production run to be completed one week ahead of schedule, ensuring Life Supplies could continue fulfilling orders without any stock shortages.
Materials & Logistics
Since materials arrived separately, TubeWorx managed the logistics carefully to prevent delays and ensure a smooth production workflow.
• Toothpaste – Delivered in IBC tanks, requiring a last-minute adapter to connect to the filling machine.
• Aluminium tubes – A rare design with a snap-off nozzle rather than a screw cap, requiring careful handling during filling.
• Packaging – Provided by Life Supplies, consisting of individual tube boxes that needed to be assembled before filling.
• Shipping and storage – Any unused materials had to be packed and shipped back after production was completed.
By using 100% aluminium tubes, Life Supplies reinforced their commitment to sustainability. Unlike plastic, aluminium is infinitely recyclable, helping reduce plastic waste. Additionally, aluminium gives a more premium aesthetic and feel, making the product stand out in the personal care market.
By using 100% aluminium tubes, Life Supplies reinforced their commitment to sustainability. Unlike plastic, aluminium is infinitely recyclable, helping reduce plastic waste. Additionally, aluminium gives a more premium aesthetic and feel, making the product stand out in the personal care market.
The Solution
Preparation and Problem-Solving
Before production could begin, TubeWorx needed to ensure that all potential issues were addressed upfront. Careful preparation was key to keeping everything on schedule.
One of the first steps was resolving the overfilling issue that Life Supplies had previously encountered. After reviewing their past production challenges, we confirmed that excessive fill levels were the cause of the problem. To prevent this from happening again, TubeWorx tested and established the correct toothpaste fill level before running the first batch. The machines were recalibrated accordingly to ensure precise, consistent filling.
Another major challenge was the non-standard IBC fitting that arrived with the toothpaste. Since it was incompatible with our equipment, TubeWorx had to urgently source and install a custom adapter to allow smooth product transfer. Additionally, the unique snap-off nozzle tube design required special handling to prevent damage during the filling process. Our team tested and adjusted the filling setup to ensure that the tubes could be processed safely and efficiently.
To avoid delays, logistics had to be carefully planned. The materials—toothpaste, aluminium tubes, and packaging—arrived separately, meaning their arrival had to be coordinated to keep production running without interruptions. Any leftover materials also had to be organized and shipped back to the client after production was complete.
Before production could begin, TubeWorx needed to ensure that all potential issues were addressed upfront. Careful preparation was key to keeping everything on schedule.
One of the first steps was resolving the overfilling issue that Life Supplies had previously encountered. After reviewing their past production challenges, we confirmed that excessive fill levels were the cause of the problem. To prevent this from happening again, TubeWorx tested and established the correct toothpaste fill level before running the first batch. The machines were recalibrated accordingly to ensure precise, consistent filling.
Another major challenge was the non-standard IBC fitting that arrived with the toothpaste. Since it was incompatible with our equipment, TubeWorx had to urgently source and install a custom adapter to allow smooth product transfer. Additionally, the unique snap-off nozzle tube design required special handling to prevent damage during the filling process. Our team tested and adjusted the filling setup to ensure that the tubes could be processed safely and efficiently.
To avoid delays, logistics had to be carefully planned. The materials—toothpaste, aluminium tubes, and packaging—arrived separately, meaning their arrival had to be coordinated to keep production running without interruptions. Any leftover materials also had to be organized and shipped back to the client after production was complete.
Filling and Sealing
Once the preparation phase was complete, the filling process began. The toothpaste was pumped directly from the IBC tank into the filling machine’s hopper, ensuring a smooth and hygienic transfer.
The filling machine was able to operate at an efficient speed of 36 tubes per minute, ensuring both accuracy and speed. Each tube was precisely filled to the newly calibrated level, eliminating the risk of overfilling. Immediately after filling, the tubes moved along the conveyor to the sealing and crimping stage, where adjustments had been made to accommodate the tube height and maintain a secure, professional seal.
To ensure full traceability and quality control, each tube was stamped with a batch code, allowing Life Supplies to track production details if needed.
Since the tubes were packed into individual boxes, pre-assembly was essential to maintaining a smooth workflow. To keep up with the filling speed, TubeWorx had prepared these boxes in advance, ensuring that once the tubes came off the line, they could be immediately packed into their retail packaging. The boxed tubes were then bulk-packed into larger boxes, ready for palletization.
Once everything was packed, the completed pallets were shipped to multiple fulfillment centers based on Life Supplies’ distribution requirements. TubeWorx handled the coordination of deliveries, ensuring the right quantities reached the right destinations on time. Any surplus materials were also packed and shipped back to the client.
Since the tubes were packed into individual boxes, pre-assembly was essential to maintaining a smooth workflow. To keep up with the filling speed, TubeWorx had prepared these boxes in advance, ensuring that once the tubes came off the line, they could be immediately packed into their retail packaging. The boxed tubes were then bulk-packed into larger boxes, ready for palletization.
Once everything was packed, the completed pallets were shipped to multiple fulfillment centers based on Life Supplies’ distribution requirements. TubeWorx handled the coordination of deliveries, ensuring the right quantities reached the right destinations on time. Any surplus materials were also packed and shipped back to the client.
Once the preparation phase was complete, the filling process began. The toothpaste was pumped directly from the IBC tank into the filling machine’s hopper, ensuring a smooth and hygienic transfer.
The filling machine was able to operate at an efficient speed of 36 tubes per minute, ensuring both accuracy and speed. Each tube was precisely filled to the newly calibrated level, eliminating the risk of overfilling. Immediately after filling, the tubes moved along the conveyor to the sealing and crimping stage, where adjustments had been made to accommodate the tube height and maintain a secure, professional seal.
To ensure full traceability and quality control, each tube was stamped with a batch code, allowing Life Supplies to track production details if needed.
Inspection, Packaging, and Shipping
Quality control was a priority throughout the process. Every filled tube underwent inspection for weight accuracy, seal integrity, and batch coding before moving to the next stage.
Quality control was a priority throughout the process. Every filled tube underwent inspection for weight accuracy, seal integrity, and batch coding before moving to the next stage.
Since the tubes were packed into individual boxes, pre-assembly was essential to maintaining a smooth workflow. To keep up with the filling speed, TubeWorx had prepared these boxes in advance, ensuring that once the tubes came off the line, they could be immediately packed into their retail packaging. The boxed tubes were then bulk-packed into larger boxes, ready for palletization.
Once everything was packed, the completed pallets were shipped to multiple fulfillment centers based on Life Supplies’ distribution requirements. TubeWorx handled the coordination of deliveries, ensuring the right quantities reached the right destinations on time. Any surplus materials were also packed and shipped back to the client.
Inspection, Packaging, and Shipping
Quality control was a priority throughout the process. Every filled tube underwent inspection for weight accuracy, seal integrity, and batch coding before moving to the next stage.
Quality control was a priority throughout the process. Every filled tube underwent inspection for weight accuracy, seal integrity, and batch coding before moving to the next stage.
Since the tubes were packed into individual boxes, pre-assembly was essential to maintaining a smooth workflow. To keep up with the filling speed, TubeWorx had prepared these boxes in advance, ensuring that once the tubes came off the line, they could be immediately packed into their retail packaging. The boxed tubes were then bulk-packed into larger boxes, ready for palletization.
Once everything was packed, the completed pallets were shipped to multiple fulfillment centers based on Life Supplies’ distribution requirements. TubeWorx handled the coordination of deliveries, ensuring the right quantities reached the right destinations on time. Any surplus materials were also packed and shipped back to the client.
The Outcome
Thanks to careful planning, precise execution, and fast problem-solving, the entire production run was completed one week ahead of schedule. This allowed Life Supplies to restock their inventory before running out of stock, avoiding any disruption to customer orders.
The recalibrated fill level eliminated the overfilling issue, ensuring a better customer experience by preventing unwanted product wastage. The unique snap-off nozzle tubes were handled with care, preventing damage during filling and maintaining their functionality.
From start to finish, the project highlighted the importance of flexibility, technical expertise, and efficient logistics. TubeWorx successfully delivered 15,000 high-quality, retail-ready aluminium toothpaste tubes within just three weeks—demonstrating our ability to meet tight deadlines without compromising on quality.
The recalibrated fill level eliminated the overfilling issue, ensuring a better customer experience by preventing unwanted product wastage. The unique snap-off nozzle tubes were handled with care, preventing damage during filling and maintaining their functionality.
From start to finish, the project highlighted the importance of flexibility, technical expertise, and efficient logistics. TubeWorx successfully delivered 15,000 high-quality, retail-ready aluminium toothpaste tubes within just three weeks—demonstrating our ability to meet tight deadlines without compromising on quality.
Conclusion
The Life Supplies project showcased TubeWorx’s ability to handle complex filling challenges while maintaining efficiency and precision. By solving technical issues, optimizing logistics, and ensuring strict quality control, we not only met but exceeded the client’s expectations.
Looking for a trusted partner for your tube filling needs? Contact Tubeworx today!
++44 (0)1223 625253
sales@tubeworx.co.uk
Tubeworx Ltd. Haynes' Yard, Swaffham Road, Cambridge, CB25 9EZ